Loading
Belt conveyors or vibration machines
Depending on the type of catalyst, the manufacturer’s specifications and the structural conditions of the tubular reactor, T.I.M.E. Service uses different loading systems. Depending on the type of catalyst and if there are different catalyst bulk materials in the individual tubes, either belt conveyors are used to load 8 parallel tubes or vibration machines are used to load 10 parallel tubes. Both technologies are designed for gentle handling and individual loading requirements, while saving time.
Priority is given to uniform loading of all tubes in a bundle. After loading, each tube must have the same volume, deltaP and density.
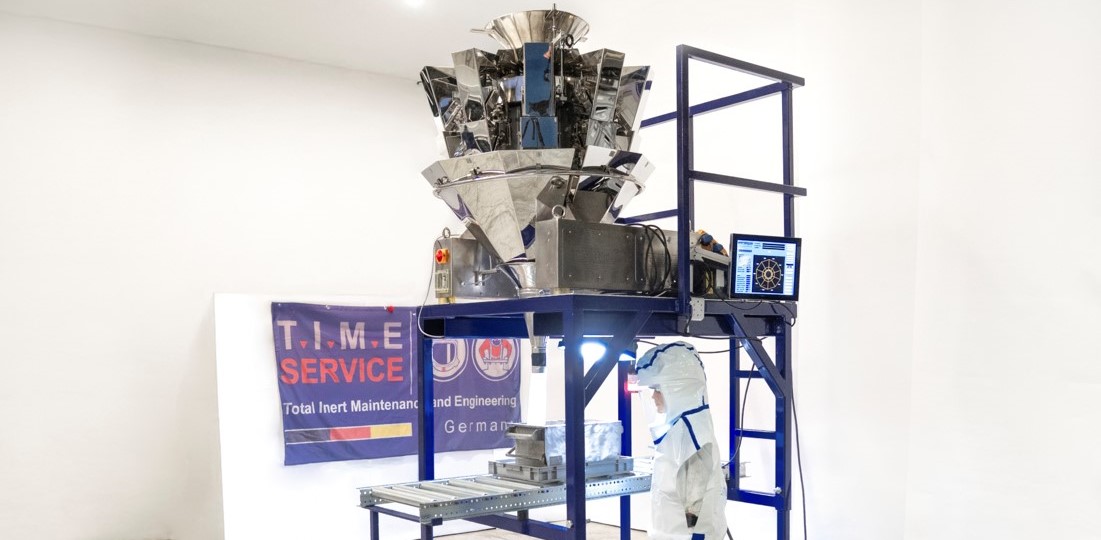
Loading of loose catalyst with multihead combination weigher
With the multihead combination weigher, unmixed catalyst can be weighed exactly to the required filling weight for filling tubular reactors. By using the multihead combination weigher, it is no longer necessary to pack the catalyst in plastic bags beforehand, thus avoiding the packaging waste that is usually generated. When using the multi-head combination weigher, the loading cartridges of the loading machines used are gently filled with the predefined catalyst weight at a filling station next to the reactor and then transported to the loading machines. Continuous weighing from 30 – 2000 grams, with a tolerance of +/- 1 gram, is easily possible with 50 – 55 weighing processes per minute. Larger weights of up to 5000 grams are also possible with a multiple discharge, whereby the cycle output is reduced accordingly.
Insert Loading
T.I.M.E. Service uses insert loading for the loading of tubular reactors by means of measuring tubes. This requires that each tube is loaded with only one type of catalyst. This is the case, for example, with ethylene oxide (EO) reactors.
With our improved loading technology, we are able to achieve precise loading heights without losses due to final vacuuming. The aim is to increase the volume in the tubes by 2 to 3%, achieve the prescribed fixed level in each tube and eliminate dP variations. This is achieved by active dedusting prior to loading, customised measuring tube design and loading speed.
The complete tube sheet is laid out with inserts whose specifications have been calculated in advance for the particular reactor and catalyst.